Safety of Flight - Autopilot servo arm screws
- 4kilo
- RB's First
- Posts: 227
- Joined: Mon Nov 08, 2004 10:32 am
- Location: GPM (Grand Prairie, Texas)
- Contact:
Safety of Flight - Autopilot servo arm screws
Cross post from "The Other Side"
It was a beautiful day here in the DFW area, so I decided to take my 8 up just to bore holes in the sky. After doing a few clearing turns, I started a loop. Up I went into the "delirious burning blue" and over the top just enjoying the wonderful view, then down the backside reducing the power as the speed increased and releasing a little back pressure.
The next feeling I had is really difficult to describe. As I released the back pressure, the G-load just increased. The first thought that went through my head was "Wow, that feels wierd." Then I pushed forward on the stick, and the G-load kept increasing. As the nose came through the horizon, I put both hands on the stick and pushed hard, and by now my thought was, "Oh $^&#!" The nose kept moving up, so I pushed the power back in to maintain airspeed and rolled the lift vector off to the left to keep the nose down and the airspeed to reasonable levels.
For the next few minutes I was able to modulate the airspeed and attitude with the bank angle, while using throttle to maintain altitude. I distinctly remember thinking, "Why is my #%&$ parachute in my apartment and not on my back!" The airplane just had its first condition inspection about 6 flight hours ago last week, and I was trying to figure out what could be causing the elevator jam. I reached behind me to the rear stick to feel if it was fouled on something, but it seemed completely clear. I felt all the linkages on the front stick I could reach, but nothing was out of place. I looked back at the elevators, and both appeared completely normal, it was just that I could not deflect them down even close to neutral (about the width of the elevator horn was showing below the stab on each side). I was able to deflect them more in the up direction, but it felt like they were hitting a stop when the stick was moved forward. I tried messing with the trim, but the tab is not large enough to even partially overpower the elevators.
I next tried leveling out a little to see if it was possible to fly in level flight, but the airspeed kept decaying too far, and I certainly did not want the airplane stalling with no down elevator available. Running out of options, I put both hands on the stick and shoved really hard. Nothing. Alright, it can't get a whole lot worse, both hands and push for all I'm worth. This time the stick popped forward to about -3 G's, and I was able to recover to level flight with normal elevator feel.
To get back on the ground, I just determined to keep the airplane fast enough to keep the elevators nearly neutral, figuring that as long as I didn't get too close to the same position they jammed in, they would continue work normally. I flew a wide, low pattern at 110 knots, and touched down at about 100, which actually worked out just fine. As I slowed to taxi speed, my habit of pulling the stick aft for ground ops jammed the elevators again.
Back in the hangar, I found the problem. The arm of my autopilot elevator servo is held on by a screw, which was missing in action. The arm and attached linkage then dropped between the elevator bellcrank mounting bracket and the body of the servo and jammed there.
The screw which holds the arm on a TruTrak autopilot servo is a #8 panhead stainless 1/4 inch long, with a nylon washer between the screw head and the servo arm. This is the factory set-up, and I have never seen any indication of people using anything different. I am looking for a source for a screw with a drilled head so that I can safety the screw to the arm. I will not fly my airplane again until there is some positive safety lock on these screws (there is another identical servo for my ailerons).
Please note that there was no failure of any other aspect of the autopilot system, and I continue to have full confidence in my TruTrak autopilot. I just will require a positive safety lock on that servo arm attach screw.
Please check those screws!!! I am off to do laundry,
Pat
It was a beautiful day here in the DFW area, so I decided to take my 8 up just to bore holes in the sky. After doing a few clearing turns, I started a loop. Up I went into the "delirious burning blue" and over the top just enjoying the wonderful view, then down the backside reducing the power as the speed increased and releasing a little back pressure.
The next feeling I had is really difficult to describe. As I released the back pressure, the G-load just increased. The first thought that went through my head was "Wow, that feels wierd." Then I pushed forward on the stick, and the G-load kept increasing. As the nose came through the horizon, I put both hands on the stick and pushed hard, and by now my thought was, "Oh $^&#!" The nose kept moving up, so I pushed the power back in to maintain airspeed and rolled the lift vector off to the left to keep the nose down and the airspeed to reasonable levels.
For the next few minutes I was able to modulate the airspeed and attitude with the bank angle, while using throttle to maintain altitude. I distinctly remember thinking, "Why is my #%&$ parachute in my apartment and not on my back!" The airplane just had its first condition inspection about 6 flight hours ago last week, and I was trying to figure out what could be causing the elevator jam. I reached behind me to the rear stick to feel if it was fouled on something, but it seemed completely clear. I felt all the linkages on the front stick I could reach, but nothing was out of place. I looked back at the elevators, and both appeared completely normal, it was just that I could not deflect them down even close to neutral (about the width of the elevator horn was showing below the stab on each side). I was able to deflect them more in the up direction, but it felt like they were hitting a stop when the stick was moved forward. I tried messing with the trim, but the tab is not large enough to even partially overpower the elevators.
I next tried leveling out a little to see if it was possible to fly in level flight, but the airspeed kept decaying too far, and I certainly did not want the airplane stalling with no down elevator available. Running out of options, I put both hands on the stick and shoved really hard. Nothing. Alright, it can't get a whole lot worse, both hands and push for all I'm worth. This time the stick popped forward to about -3 G's, and I was able to recover to level flight with normal elevator feel.
To get back on the ground, I just determined to keep the airplane fast enough to keep the elevators nearly neutral, figuring that as long as I didn't get too close to the same position they jammed in, they would continue work normally. I flew a wide, low pattern at 110 knots, and touched down at about 100, which actually worked out just fine. As I slowed to taxi speed, my habit of pulling the stick aft for ground ops jammed the elevators again.
Back in the hangar, I found the problem. The arm of my autopilot elevator servo is held on by a screw, which was missing in action. The arm and attached linkage then dropped between the elevator bellcrank mounting bracket and the body of the servo and jammed there.
The screw which holds the arm on a TruTrak autopilot servo is a #8 panhead stainless 1/4 inch long, with a nylon washer between the screw head and the servo arm. This is the factory set-up, and I have never seen any indication of people using anything different. I am looking for a source for a screw with a drilled head so that I can safety the screw to the arm. I will not fly my airplane again until there is some positive safety lock on these screws (there is another identical servo for my ailerons).
Please note that there was no failure of any other aspect of the autopilot system, and I continue to have full confidence in my TruTrak autopilot. I just will require a positive safety lock on that servo arm attach screw.
Please check those screws!!! I am off to do laundry,
Pat
RV-8
N804PT - IO-360, Hartzell blended airfoil, GRT dual Horizon I & EIS, TruTrak ADI Pilot II
Flying - 950 hours!
N804PT - IO-360, Hartzell blended airfoil, GRT dual Horizon I & EIS, TruTrak ADI Pilot II
Flying - 950 hours!
- Mike Balzer
- Class E
- Posts: 147
- Joined: Tue May 20, 2008 11:18 pm
- Location: Saugus, CA
Pat,
I glad to see your OK. Is there a chance you could post a picture of the bolts and hardware in the configuration your discribing. This may help me and other pilots get a better visual.
Thanks,
Mike Balzer
I glad to see your OK. Is there a chance you could post a picture of the bolts and hardware in the configuration your discribing. This may help me and other pilots get a better visual.
Thanks,
Mike Balzer
It is better to be on the ground wishing you were in the air, then being in the air and wishing you were on the ground. N78MB
- TomNativeNewYorker
- Class D
- Posts: 439
- Joined: Tue Mar 21, 2006 9:19 pm
- Location: KSAV
A lot of flight control hardware that I have experience with uses self retaining bolts. Example>> https://www.avibank.com/index.cfm?fusea ... duct_id=36
An online search didnt find any as small as 8/32, 10/32 seems to be the smallest.
Aircraft Spruce has several types of drilled head screws. I would at least use these with an MS21042-8 self locking nut.
http://www.aircraftspruce.com/catalog/h ... lister.php
http://www.aircraftspruce.com/catalog/h ... -01190.php
http://www.aircraftspruce.com/catalog/h ... 1351CH.php
http://www.aircraftspruce.com/catalog/h ... S1351H.php
http://www.aircraftspruce.com/catalog/hapages/an501.php
An online search didnt find any as small as 8/32, 10/32 seems to be the smallest.
Aircraft Spruce has several types of drilled head screws. I would at least use these with an MS21042-8 self locking nut.
http://www.aircraftspruce.com/catalog/h ... lister.php
http://www.aircraftspruce.com/catalog/h ... -01190.php
http://www.aircraftspruce.com/catalog/h ... 1351CH.php
http://www.aircraftspruce.com/catalog/h ... S1351H.php
http://www.aircraftspruce.com/catalog/hapages/an501.php
- 4kilo
- RB's First
- Posts: 227
- Joined: Mon Nov 08, 2004 10:32 am
- Location: GPM (Grand Prairie, Texas)
- Contact:
Tom,
Thanks for the links. Since the screw is threaded into the servo drive boss, there is no possibility of using a locking nut (that's the problem).
So far, it looks like the MS35265-41 screw is the best solution. All the others are too big or too long. I will try to find one locally today so I don't have to wait for delivery.
TruTrak is looking into the situation. I am still waiting to hear back from them.
Pat
Thanks for the links. Since the screw is threaded into the servo drive boss, there is no possibility of using a locking nut (that's the problem).
So far, it looks like the MS35265-41 screw is the best solution. All the others are too big or too long. I will try to find one locally today so I don't have to wait for delivery.
TruTrak is looking into the situation. I am still waiting to hear back from them.
Pat
RV-8
N804PT - IO-360, Hartzell blended airfoil, GRT dual Horizon I & EIS, TruTrak ADI Pilot II
Flying - 950 hours!
N804PT - IO-360, Hartzell blended airfoil, GRT dual Horizon I & EIS, TruTrak ADI Pilot II
Flying - 950 hours!
Holy crap Pat, all I can think of is how glad I am you kept your cool and figured out how to keep the plane flying while you sorted out your options. One heck of good job!!
Thanks for posting this, something tells me there are going to be a lot of people looking at those screws. I intend on using the TruTrak products so am very interested as I'm sure are a LOT of people.
Thanks for posting this, something tells me there are going to be a lot of people looking at those screws. I intend on using the TruTrak products so am very interested as I'm sure are a LOT of people.
Don Sinclair
CYKF
RV-7A (Fuselage)
CYKF
RV-7A (Fuselage)
- Wicked Stick
- Class B
- Posts: 1000
- Joined: Wed Feb 09, 2005 10:00 pm
- Location: KEWB
Pat,
Glad to hear you kept your wits about you and made it down safely.
This could have been a lethal situation.
Can you post pictures of your servo install ?
I'd like to compare to mine and see if all is well and safe in how I did mine.
I found 3 of the 4 small silver allen screws were loose on my pitch servo the other day. I had just finished riveting on my 872 C Flap Fairings and was looking things over before installing the baggage floor skins when I noticed it. A long time ago, I had installed the servo's and ran the wire, but only recently had I ran the servos while doing the setup procedures for the ADI Pilot II on the panel. I could have swore the servo's were fine back when I put them in.
So, I removed them and coated the threads with some blue locktite and re-installed them with a small allen wrench.
It would be great if I got to compare your install and how/what hardware you have on yours. Maybe even a pic of how and where it jammed.
Also, be sure to check all your pushrods (in pitch) for any damage caused by the amount of force you used to get it free during that flight.
Glad to hear you kept your wits about you and made it down safely.
This could have been a lethal situation.
Can you post pictures of your servo install ?
I'd like to compare to mine and see if all is well and safe in how I did mine.
I found 3 of the 4 small silver allen screws were loose on my pitch servo the other day. I had just finished riveting on my 872 C Flap Fairings and was looking things over before installing the baggage floor skins when I noticed it. A long time ago, I had installed the servo's and ran the wire, but only recently had I ran the servos while doing the setup procedures for the ADI Pilot II on the panel. I could have swore the servo's were fine back when I put them in.
So, I removed them and coated the threads with some blue locktite and re-installed them with a small allen wrench.
It would be great if I got to compare your install and how/what hardware you have on yours. Maybe even a pic of how and where it jammed.
Also, be sure to check all your pushrods (in pitch) for any damage caused by the amount of force you used to get it free during that flight.
Dave "WS" Rogers
RV-8 (125 hrs & counting)
N173DR
RV-8 (125 hrs & counting)
N173DR
What a sickening feeling! Sounds like you kept your head and did a great job. Now we know why pilots should be in good physical condition. You never know when you will get in a life or death struggle with your airplane.
Scott VanArtsdalen
Token Heretic
Nirvana Rodeo / Dudek Universal
S-6ES N612SV - GONE but not forgotten
RV-4 N311SV - SOLD
Token Heretic
Nirvana Rodeo / Dudek Universal
S-6ES N612SV - GONE but not forgotten
RV-4 N311SV - SOLD
- TomNativeNewYorker
- Class D
- Posts: 439
- Joined: Tue Mar 21, 2006 9:19 pm
- Location: KSAV
The aircraft I work on, when it comes to flight controls, most nut and bolt combination installation uses what we call pit pin bolts. The center of the head as a plunger you depress to release the ball locks at the opposite end of the bolt. After you install the bolt, release the plunger pin, and the balls extend from the sides of the bolt shank. Then a castellated nut is installed. You need to make sure to adjust any minor variances in grip length with a washer or two under the head or next to the nut. After the stackup is installed and torqued properly, the nut is then cotter pinned. You have a double fail safe here. One with the nut safetied to prevent spinning, and if for any reason, the nut dissapeared, the bolt should remain in place because of the ball locks on the bolt. I have never seen the ball locks fail in a manner that it lost the safety feature, but have seen numerous ones when depressing the plunger wouldnt release the ball locks . That is a real PITA because now you got to cut the bolt in some for or another to facilitate removal.


The other safetying methods are traditional drilled head bolts and castle/castellated nuts when the nuts are cotter pinned, and the heads get safety wired.
The last is when a bolt is screwed into a component that is threaded, such as servos, hydraulic actuators and pumps, mechanical screwjack actuators etc, the heads are pre drilled, and always safety wired together.
Remember to check the safety wire to ensure you wrapped it in the correct direction that prevents hardware from vibrating loose.
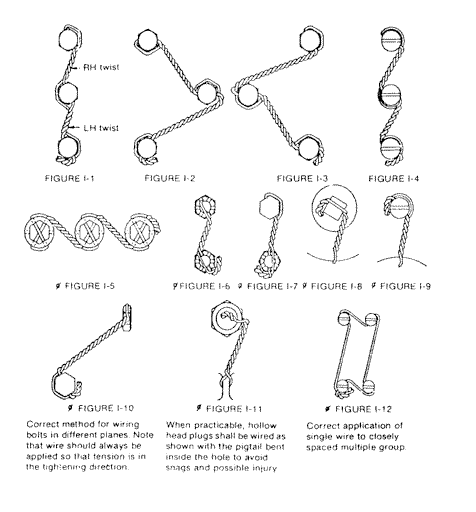
I love to safety wire, and it takes a lot of practice to get it right. Dont scrimp, get the good 301/302 stainless steel wire, it doesnt break as easy as the others and is a little more forgiving.
Lastely, dont scrimp and get cheap safety wire pliers like the ones found at flea markets or Harbor freight. The jaws tend to loosen up not long after a few uses, and makes the job harder.Once I bought a 6" and a 9" reversible pairs of safety wire pliers made by Proto, all I ever did was improve in the way the I did my safetying jobs.


The other safetying methods are traditional drilled head bolts and castle/castellated nuts when the nuts are cotter pinned, and the heads get safety wired.
The last is when a bolt is screwed into a component that is threaded, such as servos, hydraulic actuators and pumps, mechanical screwjack actuators etc, the heads are pre drilled, and always safety wired together.
Remember to check the safety wire to ensure you wrapped it in the correct direction that prevents hardware from vibrating loose.
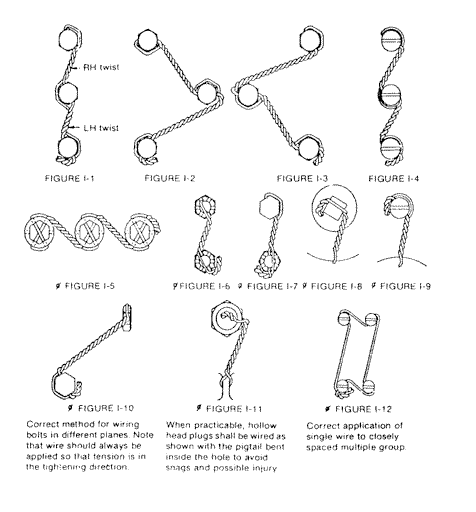
I love to safety wire, and it takes a lot of practice to get it right. Dont scrimp, get the good 301/302 stainless steel wire, it doesnt break as easy as the others and is a little more forgiving.
Lastely, dont scrimp and get cheap safety wire pliers like the ones found at flea markets or Harbor freight. The jaws tend to loosen up not long after a few uses, and makes the job harder.Once I bought a 6" and a 9" reversible pairs of safety wire pliers made by Proto, all I ever did was improve in the way the I did my safetying jobs.
- 4kilo
- RB's First
- Posts: 227
- Joined: Mon Nov 08, 2004 10:32 am
- Location: GPM (Grand Prairie, Texas)
- Contact:
Follow Up
Here is a picture of the jammed elevator servo arm:

And here is my solution:

The screw in the photo is secured with both locktite and safety wire.
I used a MS24677-14 which is a socket head cap screw with a drilled head in place of the original screw. I had to use three washers because of the length of the screw. A MS35265-41 1/4 in filister head screw would be a better choice, but I couldn't find one locally.
I discussed the situation with TruTrak this morning, and Lucas said that they would be investigating the problem.
Pat

And here is my solution:

The screw in the photo is secured with both locktite and safety wire.
I used a MS24677-14 which is a socket head cap screw with a drilled head in place of the original screw. I had to use three washers because of the length of the screw. A MS35265-41 1/4 in filister head screw would be a better choice, but I couldn't find one locally.
I discussed the situation with TruTrak this morning, and Lucas said that they would be investigating the problem.
Pat
RV-8
N804PT - IO-360, Hartzell blended airfoil, GRT dual Horizon I & EIS, TruTrak ADI Pilot II
Flying - 950 hours!
N804PT - IO-360, Hartzell blended airfoil, GRT dual Horizon I & EIS, TruTrak ADI Pilot II
Flying - 950 hours!
- TomNativeNewYorker
- Class D
- Posts: 439
- Joined: Tue Mar 21, 2006 9:19 pm
- Location: KSAV
Looking hard at your last two pics, I cant tell if all those nuts with thread locker on them have cotter keys or not.
In my opinion, every single one of those nuts or bolt heads should be cotter pinned or safety wired. Even the jam nuts on the push rods.
I sure wouldnt want to trust an adhesive on a bolt head when it comes to flight controls.
In my opinion, every single one of those nuts or bolt heads should be cotter pinned or safety wired. Even the jam nuts on the push rods.
I sure wouldnt want to trust an adhesive on a bolt head when it comes to flight controls.
- Wicked Stick
- Class B
- Posts: 1000
- Joined: Wed Feb 09, 2005 10:00 pm
- Location: KEWB
They are nylock nuts and the yellow is most likely the torque seal.
These are used on the aileron, elevator and rudder hinge bolts also.
Would you also change those to be cotter pin'd ?
To me, as long as the nylock nuts are good, and the pivot is on the bearing and not turning the bolt, all should be fine.
These are used on the aileron, elevator and rudder hinge bolts also.
Would you also change those to be cotter pin'd ?
To me, as long as the nylock nuts are good, and the pivot is on the bearing and not turning the bolt, all should be fine.
Dave "WS" Rogers
RV-8 (125 hrs & counting)
N173DR
RV-8 (125 hrs & counting)
N173DR
- TomNativeNewYorker
- Class D
- Posts: 439
- Joined: Tue Mar 21, 2006 9:19 pm
- Location: KSAV
As a mechanic I have no personal experience with nylock nuts on aircraft. We are not allowed to use them, I think heat is one of the reasons why we dont. When we use locking nuts, we use the all metal ms21042 type with the dry film lube on them(black).Wicked Stick wrote:They are nylock nuts and the yellow is most likely the torque seal.
These are used on the aileron, elevator and rudder hinge bolts also.
Well since I am not a pilot, only a mechanic and not hands on experienced with RV's I can only offer an opinion based on what I have seen in the past.Wicked Stick wrote: Would you also change those to be cotter pin'd ?
Screws, nuts, bolts, hi-lock collars and other types of threaded fasteners do vibrate loose.
Think about murphys law. Only 6 flight hours have passed since major inspection. Was this something not covered on the inspection, something that may have been overlooked, or something that developed since? Something bad happened, but it could have been much worse.
Got to also remember I work on a twin engine turboprop engine with 5100 shaft horsepower each, so your mileage may vary when it comes to vibration.
You see from the original post, the screw came out and could have cost the man his life. If I were building an aircraft for myself or someone else, damm straight I would shitcan those nylock nuts and make sure everything is secure either with cotter pins or safety wire.
Am I being paranoid? I doubt it, but as a mechanic(not A&P) but for the military, I have seen lots of different things happen. I am sure I wouldnt want take chances on safety.
Any reason why you wouldnt want to improve the safety of your aircraft? I doubt you wouldnt want to do this because of cost or weight factors, because it would probably be minimal in both cases.
I see ways of improvement, but is it overkill? I dont know maybe.
You are the one who has to fly the plane, tell me if you think it is overkill.
- Wicked Stick
- Class B
- Posts: 1000
- Joined: Wed Feb 09, 2005 10:00 pm
- Location: KEWB
I guess I'm basing my opinion on a mixture of:
1. Experience with it's use.
2. Amount of time and volume of RV aircraft that have flown without incident that use these kind of fasteners.
for the elevators, ailerons, rudders. At least with these areas, they are in the open and can be visually inspected before each flight.
In no way would I use them forward of the firewall or near heated areas and I whole heart'dly agree with you that in certain places, a caslte nut and cotter pin, or a lockwired bolt is a must do.
I plan to lockwire the servo arm screws as Pat did.
1. Experience with it's use.
2. Amount of time and volume of RV aircraft that have flown without incident that use these kind of fasteners.

In no way would I use them forward of the firewall or near heated areas and I whole heart'dly agree with you that in certain places, a caslte nut and cotter pin, or a lockwired bolt is a must do.
I plan to lockwire the servo arm screws as Pat did.
Dave "WS" Rogers
RV-8 (125 hrs & counting)
N173DR
RV-8 (125 hrs & counting)
N173DR
- TomNativeNewYorker
- Class D
- Posts: 439
- Joined: Tue Mar 21, 2006 9:19 pm
- Location: KSAV
- Wicked Stick
- Class B
- Posts: 1000
- Joined: Wed Feb 09, 2005 10:00 pm
- Location: KEWB
Yes, I'm sure that repeated on and off use would absolutely wear them out. I guess the question is how many times until they are no good.
Obviously, if you can hand/finger tighten them all the way on then it's junk, but if you have to wrench them tight when it gets to the insert, then I'm sure you can get more than a single use out of them.
I've seen different color'd inserts on them. Anyone know if one color is more durable a material than the other ?
Obviously, if you can hand/finger tighten them all the way on then it's junk, but if you have to wrench them tight when it gets to the insert, then I'm sure you can get more than a single use out of them.
I've seen different color'd inserts on them. Anyone know if one color is more durable a material than the other ?
Dave "WS" Rogers
RV-8 (125 hrs & counting)
N173DR
RV-8 (125 hrs & counting)
N173DR
manufacturer IIRC, no more durable.Wicked Stick wrote: I've seen different color'd inserts on them. Anyone know if one color is more durable a material than the other ?
they are reuseable as long as you cant install them with finger pressure.
i never reuse them. and i rarely reuse bolts

william....don't let it beat you down, you are stronger than you think.
i feel much same as you, so a few months back, maybe a year ago, i ordered all the bolts with an "a" in the p/n. this getes them a cotter pin hole and i also ordered those damn 50 cent a piece castelatted nuts with the non metallic self locking insert. the thing is they only have a few complete threads. 3 tops. i did'nt like that much. then your onto custom fitting with washers or overtorquing them for proper cotter pin alignment.TomNativeNewYorker wrote:
You see from the original post, the screw came out and could have cost the man his life. If I were building an aircraft for myself or someone else, damm straight I would shitcan those nylock nuts and make sure everything is secure either with cotter pins or safety wire.
well long story short the nylocs aint going anywhere and the adding and removing washers for cotter pin alignment is way to damn aggravating.
i never gave much though to a all metal lock nut..i wish i would have because i feel i wuld have been plenty happy with that.
not that it matters but, your life is in very much the same danger at the highway speeds we travel these days (90+) and all of the front ends have self locking nuts holding them together and lug nuts are simpley torqued to 100- 140 ft lbs. if at all.

william....don't let it beat you down, you are stronger than you think.
- TomNativeNewYorker
- Class D
- Posts: 439
- Joined: Tue Mar 21, 2006 9:19 pm
- Location: KSAV
I guess I just have a different point of view seeing how things are on an E-2c Hawkeye as a mechanic.weezbad wrote:
i feel much same as you, so a few months back, maybe a year ago, i ordered all the bolts with an "a" in the p/n. this getes them a cotter pin hole and i also ordered those damn 50 cent a piece castelatted nuts with the non metallic self locking insert.
I am not a builder, and probably never will, so I just have an alternate type of experience to share.
I was actually pretty shocked as to what I saw in this thread with the lack of safetying compared to what I am accustomed to seeing over my career.
i was similarly shocked. i came from working on helis and everything has a secondary safety. i am still trying to implement safties on my 7. But honestly, this is the only case ive heard of and on top of that it wasnt even saftied in a primary way, much less a cotter pin. reading dynons post on VAF leads me to think the TT guys will have to implement some real change in this set up to satisfy the users. i will go dynon A/P but only because i have dynons. i wouldnt use the TT at this time. that safety wire will cause more problems than it will help, due to the shafts ability to spin and spin. right now lock tite is the only saftey for the TT.
william....don't let it beat you down, you are stronger than you think.