a conduit hanger could be a handy part. a simple part to design and make. follow along.
*********************
since we don't know the final location of the part yet, I'll add a circle and extrude it to make the conduit. the conduit location will be adjusted later.
***********************
OK, that was 10 minutes of work, need to take a coffee break.
offset the outer conduit circle .03 for clearance. then offset that circle .10 inch to make the outer ring of the hanger. draw half of the rivet mounting surface and then mirror it and extrude it .10 inch. all of these dimensions will be fine-tuned later, we are working to get the basic shape now.
OK, that was another 10 minutes, time to take a break and listen to some music.
***********************
add some holes, fillets and a chamfer. snug the conduit closer to the edge of the lightening hole. decrease the clearance to the conduit to be .04 inch diametrical. show the arrangement with two conduit tubes at 45 degrees (baseline), 30 degrees and 60 degrees.
OK, that was another 15 minutes. time to print one for a test fit and determine if I can take some weight out.
so, about 1 hr working time to do one of these from scratch at a very relaxed pace. it's just play for me now.
*************************
assume conduit hanger supports 1 lb of wire, then multiply by a g-load of 6, then multiply by 1.5 = 9 lb. the most outboard area is not doing much work and just going for the ride. opportunity to reduce weight, but we already knew that the material between bolt holes generally doesn't do much work, right? the next time you see a scalloped flange, you will know why.
************************
taking a closer look at the rivet holes to simulate compression only at rivet hole wall that is closer to the real condition. for an ultimate 9 lb loading for this part, there is some localized exceedance at the hole edge, but the bulk of the hole is within the allowable limits. the plastic material has adequate strain capability to absorb and distribute this localized stress.
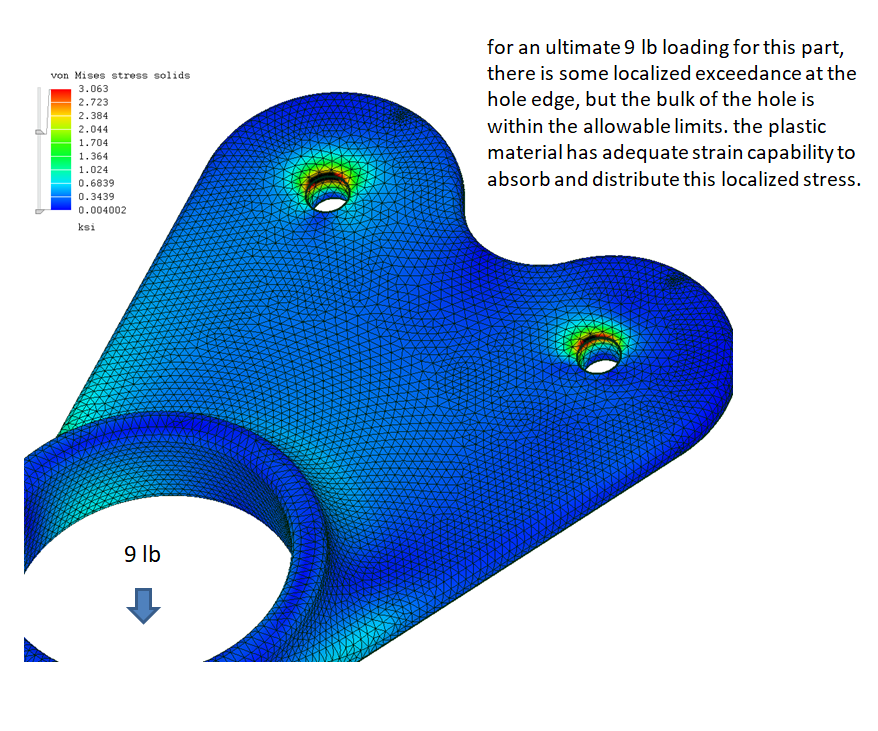
Steve Melton
N531EM, RV9A, Superior O-320, WW 200RV prop, Slick mags, CHT 330F, EGT 1300F, B&C, 1300+ hours
Freedom and Democracy are all that really matter.
Ride a bike, unlock the world.
https://www.rvplasticparts.com/