Page 1 of 1
Alumiprep Forever etching?
Posted: Wed Mar 31, 2010 2:37 pm
by 704CH
Hey guys, have any of you had this happen to you? It looks like a slight blemish or smear for now, but will continue to corrode. This is the second time this has happened and I think it is due to not complete rinse off of the alumiprep. (Yes I will rinse better from now on)
To stop it though, the only thing I can think of is to continue the skin prep in this area and prime over it. If you have a better solution, please let me know. This time it is on the outside skin luckily on the bottom of the flap but I would rather not prime outside skin until I paint. If I leave it, then it will continue to etch and eventually be fairly significant. That is what happened on my HS.
thx
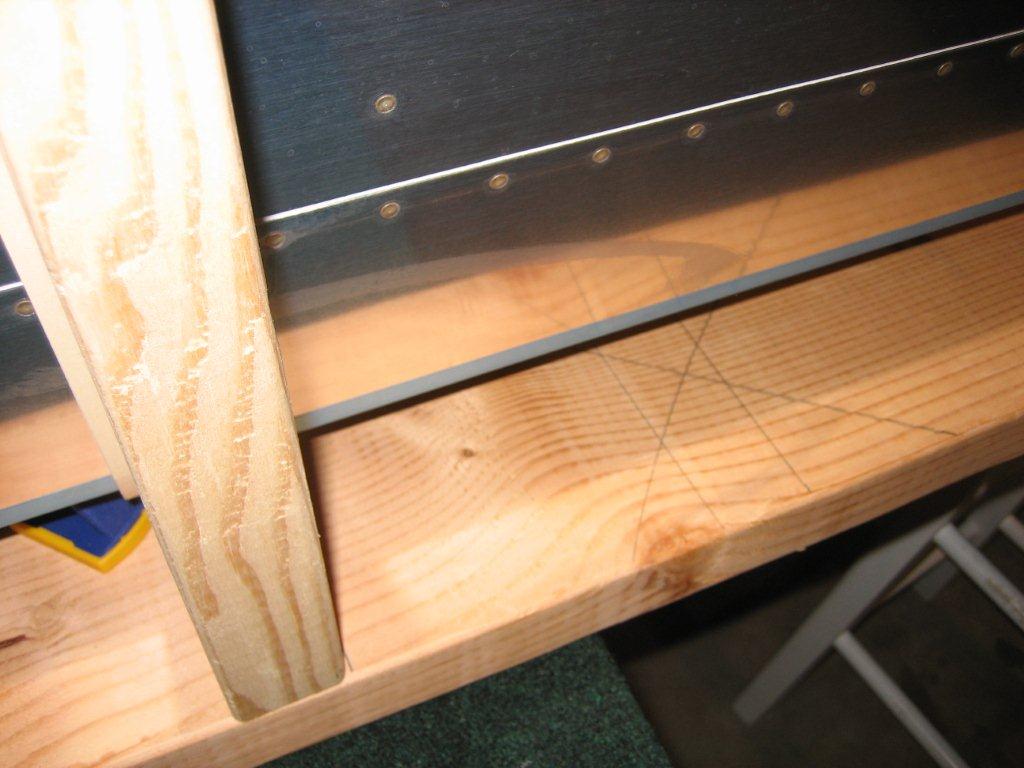
Posted: Fri Apr 02, 2010 8:35 am
by TomNativeNewYorker
Hard to tell from the pic, but it looks like you just need to wet it down, scotch brite it to get the water break free and do it again.
sometimes, the best way to tell that you have it rinsed off properly is to check the rinse water running off with some pH paper.
Posted: Fri Apr 02, 2010 8:48 am
by TomNativeNewYorker
Some basics on treatment of aluminum. Please dont ask the source of the manual.
SURFACE TREATMENT
5-1. PURPOSE. A critical step in the corrosion prevention and control process is the surface treatment of the metal with a prescribed chemical to form a protective oxide film. Properly applied chemical treatment imparts considerable corrosion resistance to the metal, and greatly improves the adhesion of subsequently applied paints or other coatings. Epoxy primers, for example, which do not adhere well to bare aluminum, adhere very well to chemical conversion coatings. See Table 5-1 for recommended materialsand procedures for prepaint treatments of specific metal.
5-2. SURFACE PREPARATION.
After completing corrosion removal in accordance with Chapter 4, proceed as follows:
NOTE Aircraft that have been waxed, particularly with silicone based material, may require special cleaning to obtain a surface free of water breaks. When silicone wax is suspected, solvent clean using an approved cleaning solvent and perform paragraphs 5-2.c. and 5-2.d.
a. Feathering edges of paint. Feathering of paint along the edge of areas that have been chemically or mechanically stripped is required prior to pre-treatment and repainting to ensure a smooth, overlapping transition between the old and new paint surfaces. The
smooth, overlapping paint film will ensure the absence of a rough, soil accumulating junction between the old Alloy Surface Treatment Procedure Aluminum alloys MIL-DTL-81706 Class 1A (Form III - ready to use premixed liquid) Immerse part for two to four minutes, use sponge stick applicator, or brush until an irridescent yellow color is obtained. Immediately rinse part thoroughly. Allow to dry (usually eight hours, but do not exceed 72 hours) before painting. See NOTE (1).
Touch-N-PrepTM Pen Brush clean surface using the acrylic tip of the pen to apply a MIL-DTL-81706 conversion coating. The treated surface does not require rinsing. Magnesium alloys AMS M-3171 Type VI (chromic acid brush-on treatment) Apply chemical conversion coating materials to surface using a brush. Keep the surface wet with treatment material until a color change is noticed (approximately 1 to 3 minutes). Depending upon the magnesium alloy, the color change will vary from golden-brown, greenish-brown, brassy to gray. After the color change, rinse treated surfaces with clean, fresh water and allow drying completely before painting. See NOTE (1).
Ferrous metals (other than stainless steel) None (Treatment prior to painting is limited to corrosion removal and cleaning.) Stainless steel and nickel alloys None Copper alloys None (NOTE (2)) Titanium alloys None (NOTE (2)) Plated and phosphated cadmium
None Solvent wipe to clean the surface.
NOTE (1)
Drying time may be accelerated by blowing with filtered warm air. However, if the air contains oil (from a compressor) or other impurities, the paint which is applied will not pass tape adhesion tests and will probably peel leading to additional corrosion. Drying air temperature should be no more than 140° F (60° C) or conversion coating will degradate and lose its effectiveness. NOTE (2) Treatment is limited to corrosion removal and cleaning. These surfaces are not normally painted, but may require painting for decorative purposes, or in instances where the surface will be in contact with a dissimilar anodic metal. Corrosion preventive compounds (CPCs) may be applied as recommended in Chapter 8.