So many have filter air box wear,
and I do not. I spent a couple hours this morning and ran some simple numbers for intake pulses and compared the air box frequency response with and without filter weight. The air box fiberglass thickness was assumed to be .050-inch thickness. This should be close, but I am not sure what it actually is because I have not measured it. I calculated the intake pulse frequency at 2700 rpm to be 90 Hz. A safe frequency would have 20% margin and be 108 Hz or higher.
What I found was the stock part does not appear to have sufficient frequency margin and may develop a resonant response leading to high wear. In my case, during the original build, I laid in about 12 plies of fiberglass total at the lower surfaces to stiffen this region, some to inside to help keep the filter centered. At 1300+ hours, I do not have any wear. So, the message is to stiffen the lower surface of the filter air box to raise the frequency response above the driving intake pulse frequency. It needs to be above 108 Hz. note: adding stiffening to the middle of the bottom plate that extends to the edges is the best bang for the buck, less so for just the edges.
Perhaps this analysis will help someone. You get what you paid for it.
Da Movie... everyone likes a movie. It looks like it is breathing. listen to this while you watch the movie.
Paul Simon - Kodachrome (Official Audio)
https://youtu.be/8rlDTK6QI-w?si=pDiX3beSZU6QIVgM
***************
Frequency response:
1. with no filter = 95 Hz
2. with E-3260 filter = 61 Hz
No filter
With Filter
Mass added at nodes to simulate filter weight. A simplistic approach as this gets complicated but shows a frequency trend direction.... downwards. Not good.
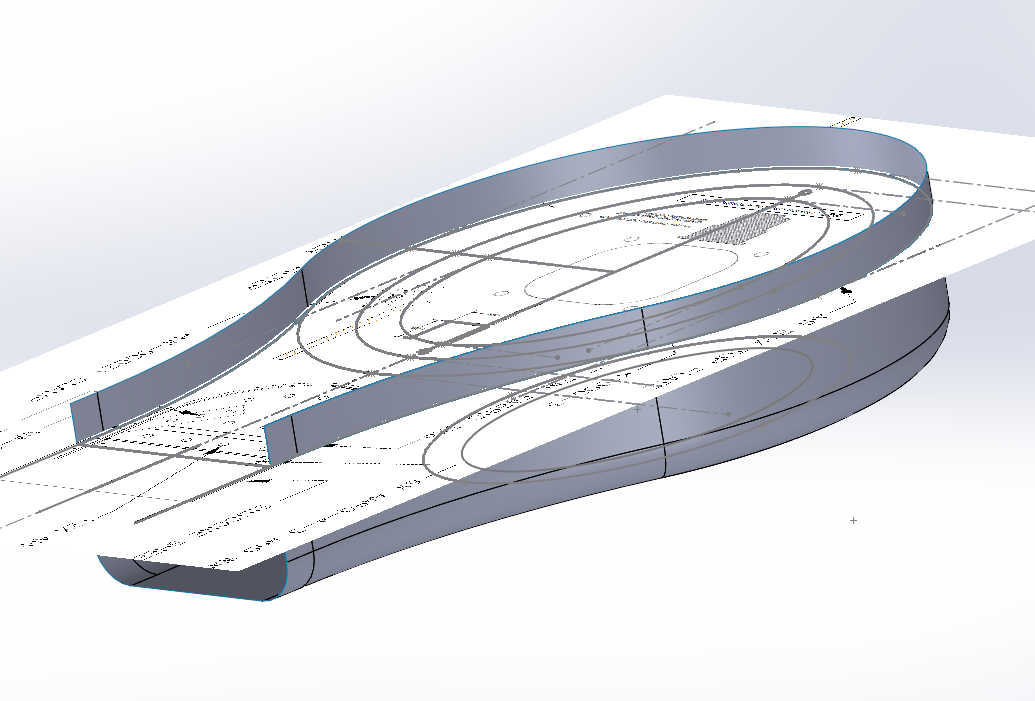